The Significance of Fund Transfers in Manufacturing Efficiency
The manufacturing process is a complex journey, starting with sourcing raw materials and ending with delivering final products that meet the demands of consumers worldwide.
The efficiency and timing of fund transfers plays a pivotal role, ensuring that every production phase is executed on time. The importance of supply chain management (SCM) becomes paramount in this intricate web of transactions and operations.
Effective supply chain management ensures that raw materials are delivered on time, production schedules are met, and products are distributed efficiently. Integrating well-managed fund transfers within these processes is not just a convenience; it’s necessary to maintain the flow and integrity of the manufacturing pipeline.
Understanding Supply Chain Management (SCM) in Manufacturing
What is Supply Chain Management?
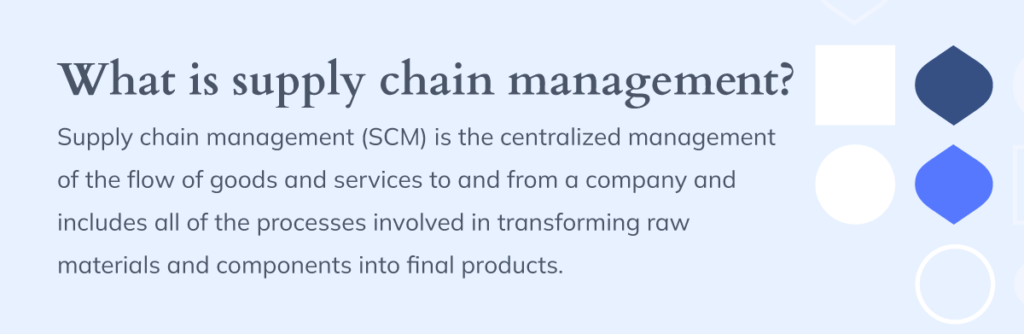
Supply Chain Management (SCM) is the art and science of coordinating and managing all the activities involved in sourcing, procuring, converting, and logistics; supply chain management involves everything.
In manufacturing, supply chain management involves the detailed coordination to move a product from supplier to customer.
Effective supply chain management streamlines everything from day-to-day product flows to unexpected natural disasters. Ensuring the manufacturing process remains efficient and responsive to customer needs and market demand.
The Crucial Role of Supply Chain Professionals
Supply chain professionals are indeed the unsung heroes of the manufacturing world. Their role extends far beyond basic management; they are the conductors of a complex system.
These professionals are entrusted with the planning, implementation, and control of various other supply chain management activities, each critical to the smooth operation of the manufacturing cycle.
In the field of procurement, supply chain management experts are responsible for negotiating contracts with suppliers. This task is crucial for securing raw materials at the best possible prices and terms, directly affecting the manufacturing cost. For example, a supply chain manager who successfully negotiates a contract for steel at a lower price can significantly reduce the production costs of an automotive manufacturing company, making its vehicles more competitive in the market.
Their responsibilities include managing relationships with logistics partners, which is vital for the amount turning raw materials of these materials. For example, a supply chain professional with a strong relationship with a logistics company can ensure priority shipping for critical components, avoiding potential production halts in an electronics manufacturing plant.
Overseeing the transportation of raw materials and finished products is a significant part of their role. This aspect involves coordinating with various transportation companies and ensuring that the transportation is cost-effective and efficient.
Efficient transportation management can reduce lead times and ensure products reach the market faster. For example, a supply chain manager might optimize the shipping routes for a clothing manufacturer, significantly reducing the time it takes to transport garments from the factory to retail outlets, thus responding quickly to fashion trends.
Key Supply Chain Models and Strategies
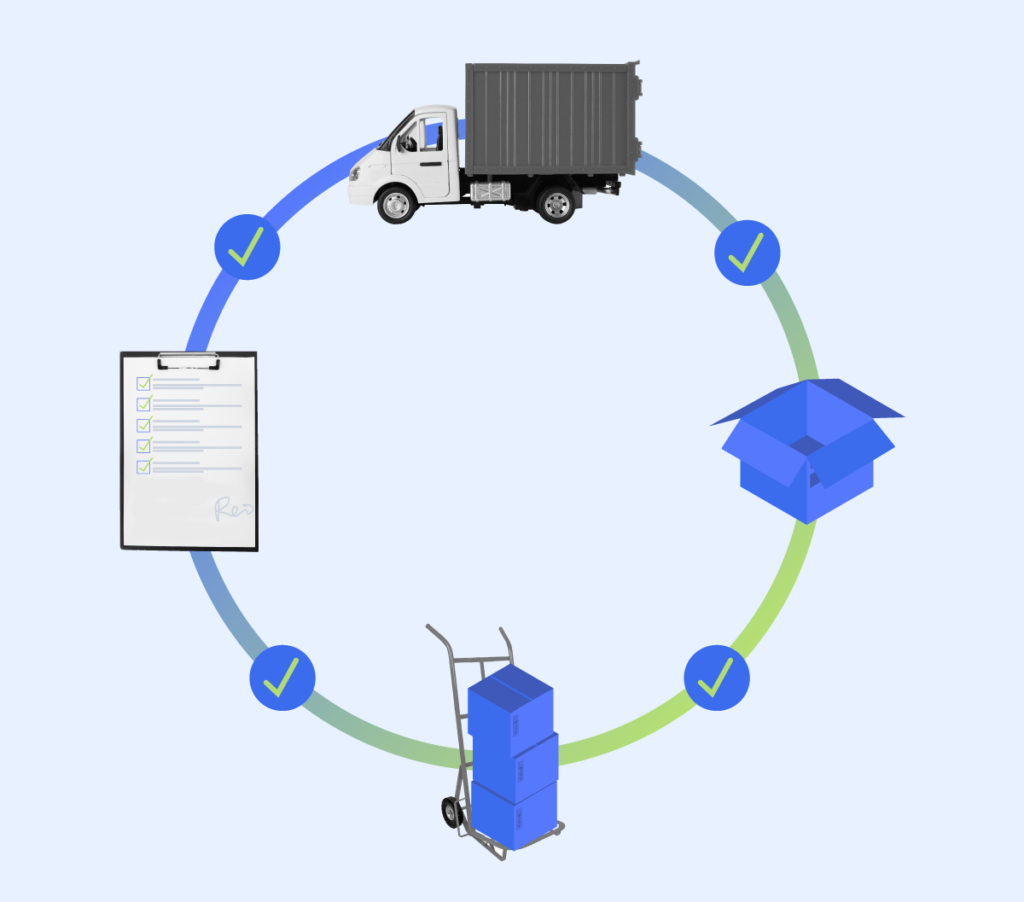
Supply Chain Management (SCM) is characterized by many models and strategies, each crafted to address specific business challenges and market dynamics. Prominent among these are the lean supply chain, agile supply chain, and custom-configured supply chain.
1. Lean supply chain
This model focuses on minimizing waste within the supply chain while maximizing productivity. It aims to streamline operations, reduce surplus inventory, and improve the overall efficiency of the manufacturing process. A lean supply chain relies heavily on precise timing and efficient resource management. By using Bancoli’s Global Business Account, companies can ensure timely payments to suppliers, which is critical in maintaining lean inventory levels and avoiding overproduction or stockouts.
2. Agile supply chain
Agility in supply chain management is about being flexible and responsive to market changes and demands. This model is particularly useful in industries where customer preferences can change rapidly. The agile supply chain requires fast decision-making and adaptability, which are supported by Bancoli’s multi-currency features. This feature allows for quick international payments in any type of currency. Enabling businesses to change demand dynamics, deliver goods on time and adapt to making seamless payments.
3. Custom-configured supply chain
This approach involves tailoring the supply chain to meet the business’s and its customers’ specific needs. It often combines elements of both lean and agile models, providing a balanced approach to managing inventory, production, and distribution.
To prepare for and manage supply chain disruptions, manufacturers should take measures that address both internal and external risks—controlling what they can control and mitigating the risk factors. This approach is integral to effective supply chain management, ensuring that the supply chain remains resilient despite unforeseen challenges. Consider and follow these supply chains’ strategies:
1. Create a risk management plan
Using the PPRR model (prevention, preparedness, response, and recovery), manufacturers take steps to avoid supply chain risks they can control, prepare a contingency plan to deal with disruptions they can’t control or hit suddenly, respond by executing preset plans to reduce a disruption’s impact.
2. Inventory management
Maintain buffer stocks of critical materials and components to mitigate short-term supply shortages.
3. Agile supply chain management
Embrace flexibility and adaptability to respond quickly to changing circumstances and unexpected events.
Integrating Advanced Technologies in Manufacturing
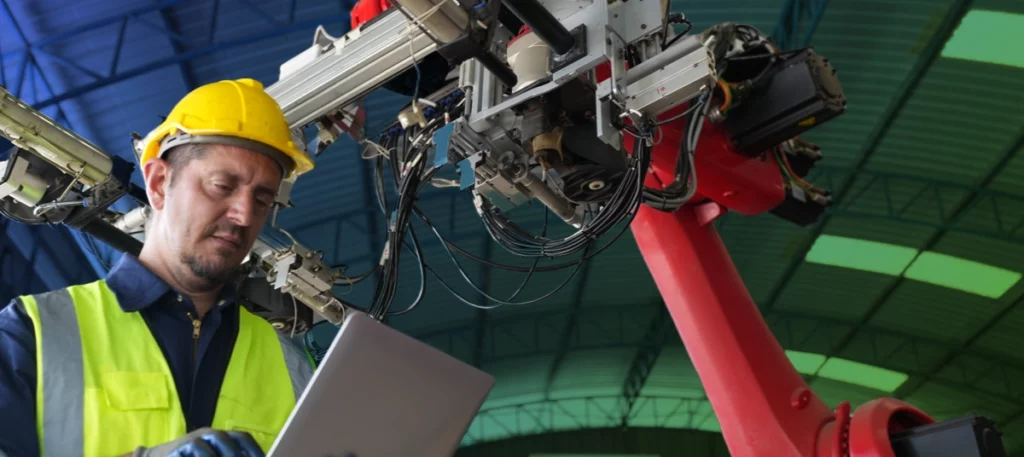
Incorporating cloud computing, machine learning, and AI into supply chains is not just a trend; it is fundamental in manufacturing operations.
Cloud technologies provide a scalable, accessible platform for managing complex data across the supply chain, enabling real-time insights and decision-making.
Machine learning and AI go a step further, offering predictive analytics capabilities that can foresee supply chain disruptions. It can also optimize the use of raw materials, and enhance the overall manufacturing process. This technological integration is pivotal in creating a more responsive and efficient supply chain.
By using Bancoli’s AI, you can enhance the comprehensive suite of services tailored to modern global business needs. This powerful component can significantly augment the effectiveness of Bancoli’s cash flow tools. Automating various stages of the invoice-to-cash process, minimize errors, and ensure timely payments.
Sustainable Practices and Risk Mitigation in SCM
Emerging technologies are increasingly prominent in promoting sustainable practices and mitigating risks in supply chain management (SCM). These technologies provide the tools needed to implement and maintain these practices throughout the supply chain.
Cloud technologies enable better tracking of sustainability initiatives, while machine learning can analyze vast amounts of data.
Additionally, these advanced technologies play a critical role in risk mitigation. By analyzing current market trends, artificial intelligence can predict potential supply chain disruptions and propose solutions to mitigate risk.
Moreover, adopting vertical integration strategies, supported by these technologies, allows for greater control over the supply chain. Further reducing risks associated with external suppliers and market volatility.
Adapting to Market Demands with Agile Manufacturing Processes
Quickly adapting to changing market demands is crucial for manufacturing success. Agile manufacturing processes, supported by advanced technologies like cloud computing and analytics capabilities, enable manufacturers to respond rapidly to changes in customer preferences and market conditions.
This agility is essential in meeting the ever-changing demands of a global market. Delays can result in lost opportunities and decreased competitiveness.
Agile manufacturing involves a holistic approach where all the processes involved in production are streamlined for quick adaptation. This approach ensures that manufacturers can pivot as needed, responding to short-term changes without sacrificing long-term goals or product quality.
Integrating these advanced technologies and adopting agile processes allow manufacturers to stay ahead of the curve. This ensures they are well-equipped to meet the demands of a dynamic market landscape.
The Impact of Timely Payments on Manufacturing
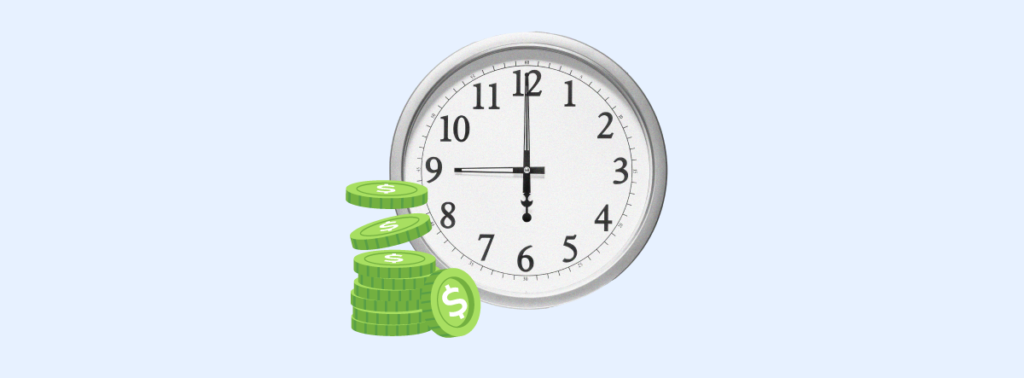
The importance of timely payments cannot be overstated in the manufacturing landscape. Effective supply chain management ensures that every financial transaction, particularly payments, is executed promptly. This is a vital element that directly influences the efficiency and success of the manufacturing process.
Ensuring Continuous Production with Effective Payment Management
This strain can lead to a reluctance to extend credit or favorable terms in the future, potentially causing bottlenecks in the entire supply chain sourcing process. In many supply chains, especially those reliant on just-in-time production, any delay in receiving raw materials can halt production lines, leading to significant losses in efficiency and productivity.
Quickly transferring funds within the supply chain is essential for seamless operations. With its Global Business Account, Bancoli facilitates the swift movement of funds, which is paramount for modern supply chains. It allows manufacturers to reliably transfer payments to suppliers, which is a crucial aspect of the supply chain management process.
This efficiency in managing payments ensures that all supply chain processes operate without interruption.
Consequences of Payment Delays in Manufacturing
Delays in the supply chain can cause a significant reaction, affecting every aspect of the manufacturing process. For instance, delaying supplier payments can lead to a hold-up in receiving necessary raw materials. This situation may occur in the automotive industry, where a delay in receiving steel can halt the entire production line.
Bancoli effectively reduces the issues associated with late payments, aligning with customer demand and market demand to ensure business success. It not only enhances relationships between supply chain partners but also aids in streamlining KYC and KYV processes.
One critical component of modern supply chains is proper and agile financial management. This includes invoice creation, processing, and the agility with which payments reach their destination.
Bancoli’s Global Business Account integrates invoicing modules and cash flow acceleration functionalities, which are favorites of sellers and buyers. This creates a win-win situation for both parties.
The primary benefit for sellers is the acceleration of cash flow. With faster processing and receipt of payments through Bancoli’s system, sellers can improve their liquidity. On the other hand, buyers benefit from the efficiency and convenience that Bancoli’s system offers.
The streamlined invoicing process makes it easier for them to track and manage their expenditures. With cash flow acceleration, buyers can also take advantage of potential early payment discounts sellers offer, leading to cost savings.
Case Study: The Ripple Effect of Delayed Payments
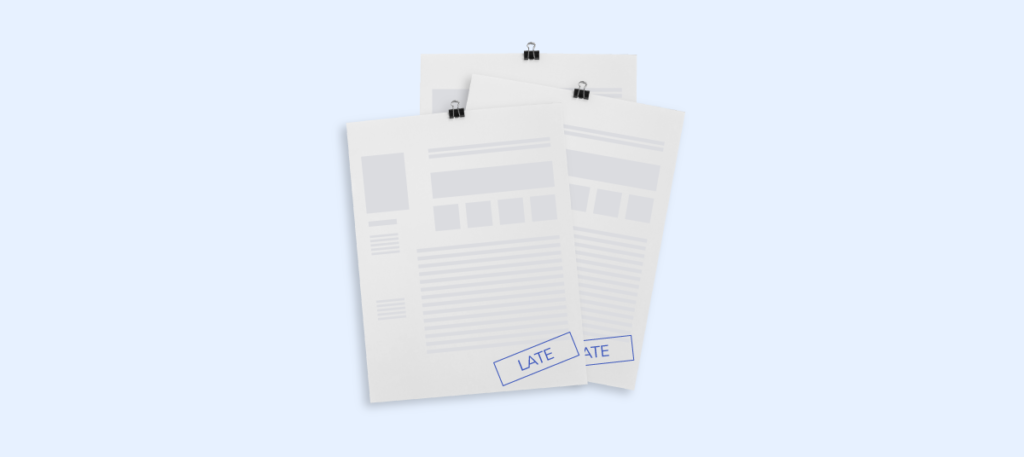
Let’s consider an example from global supply chains.
One notable case is a leading electronics company that faced significant disruptions. This delay resulted in a shortage of essential components, halting production lines and causing the company to miss crucial product launch deadlines. The ripple effect was felt throughout the entire supply chain, from the smallest supplier to the end consumer.
The company faced lower cost-efficiency, a tarnished reputation, and decreased customer loyalty. The situation emphasized the need for effective supply chain management and the importance of maintaining a steady flow of funds to ensure all entities involved can operate optimally.
These instances highlight a fundamental truth in modern manufacturing and supply chain management: the ability to improve efficiency, maintain manufacturing schedules, and satisfy market demands heavily depends on the financial fluidity within the supply chain.
When manufacturing hubs are interconnected in complex ways, the impact of financial delays can be far-reaching. Companies that recognize the importance of timely payments and incorporate practices to ensure smooth financial operations are more likely to thrive in the competitive landscape of global manufacturing.
Adopting Bancoli’s Global Business Account significantly enhances supply chain planning and management. Reduced lead times are a direct benefit, as manufacturers can quickly transfer funds, thereby speeding up the procurement of raw materials and components. This efficiency is crucial in meeting and surpassing customer expectations.
Bancoli’s Global Business Account: A Game Changer in Manufacturing
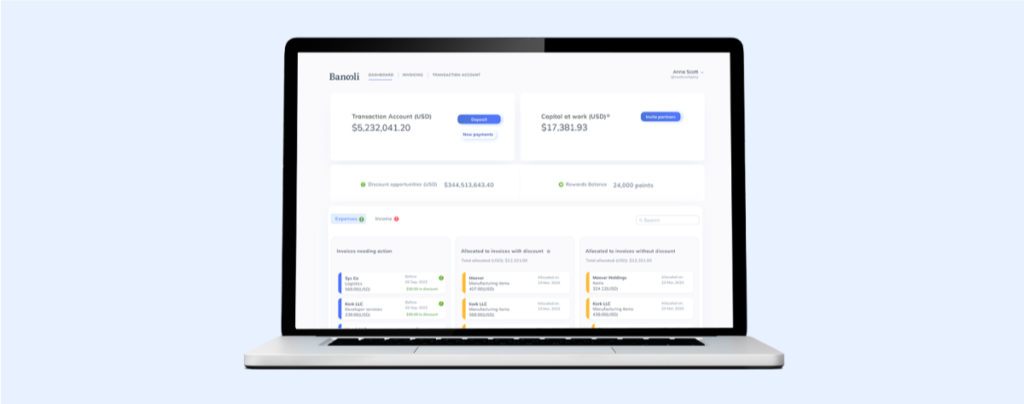
Bancoli’s Global Business Account emerges as a revolutionary tool designed to address the specific needs of modern manufacturers, offering a robust solution to old challenges of fund transfers in the supply chain.
Revolutionizing Fund Transfers with Bancoli
Bancoli’s Global Business Account is the epitome of how advanced technology and digital transformation are reshaping the financial landscape in manufacturing.
With its multi-currency features, this account simplifies and accelerates financial transactions across borders. This capability is particularly beneficial for manufacturers operating within global supply chains. Bancoli offers various features that make it an ideal choice for businesses looking to manage foreign currency cash flow efficiently.
With an easy conversion of collections in more than 25 currencies, including those that are part of Bancoli’s multi-currency business bank account. By using our GBA, companies can effortlessly manage transactions aligning with their supply chain strategy and adapting to the dynamics of international trade.
This flexibility is not just about meeting demand; it’s about exceeding it, ensuring manufacturers can respond quickly to high demand in different markets without the usual financial constraints.
Benefits of Reduced Lead Times and Improved Cash Flows
Improved cash flows are another hallmark of Bancoli’s service. With more predictable and efficient financial transactions, manufacturers can make more informed decisions, optimizing their operations for both speed and cost.
By accurately predicting and managing your cash flow with Bancoli’s solutions, you can build a reserve fund that cushions your business against the impact of late payments, ensuring operational stability.
This heightened financial agility allows manufacturers to meet demand and explore new opportunities for growth and innovation, ultimately providing a competitive advantage in a crowded market.
Strengthening Supplier Relationships Through Reliability
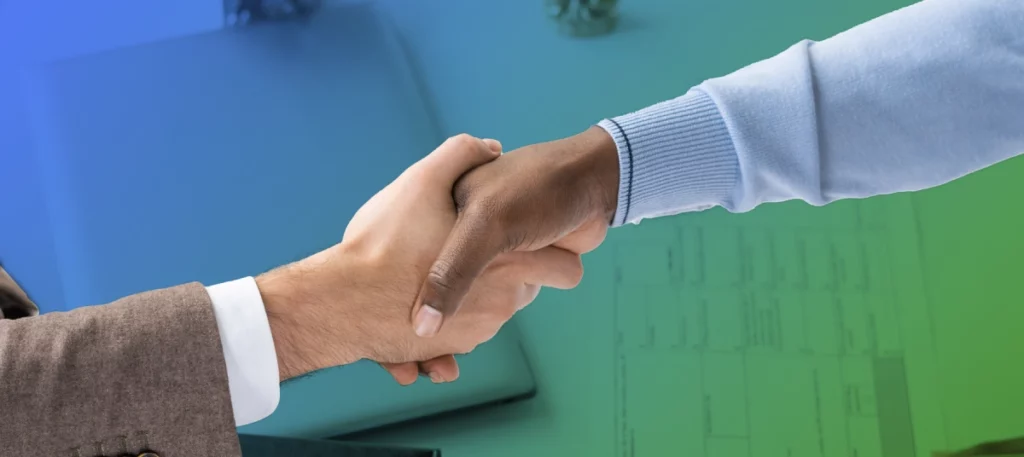
Secure payment methods offered by banks, such as encrypted transfers and robust authentication processes, ensure that every financial transaction is protected from external threats. This security is vital in preventing financial loss and fostering trust among supply chain partners. When suppliers and buyers are confident in the security of their payment solutions, it leads to stronger relationships and a more resilient supply chain.
Bancoli’s Global Business Account has USD Custody protection combined with innovative security features like ID verifications and 2-FA, making secure and seamless online payments.
Consistent and timely payments establish trust and reliability among supply chain partners, crucial for lasting partnerships. To prevent late payments, maintaining a steady cash flow is key. Bancoli’s Global Business Account helps manage multi-currency payments through automated invoice payment reminders and penalties for late payments.
By ensuring that suppliers are paid on time, Bancoli helps manufacturers maintain a robust supply chain model where each link is strong and dependable.
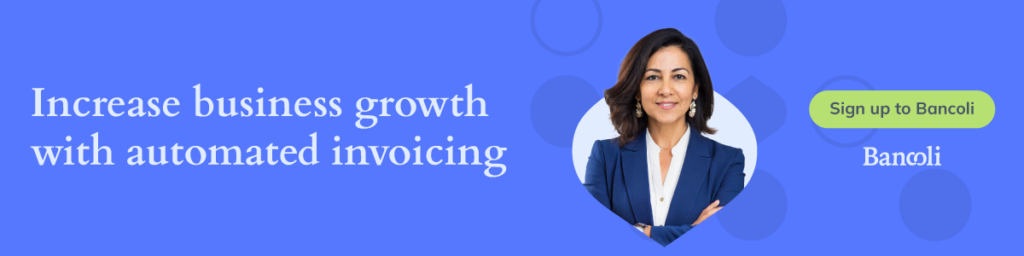
Key Takeaways: Securing Manufacturing Success with Efficient Fund Transfers
Effective supply chain management (SCM) is vital. It serves as the backbone of the manufacturing process and ensures that all elements, including those converting raw materials, material delivery, manufacture schedules, and product distribution, are efficiently managed.
Supply chain managers play a critical role in this ecosystem. They are responsible for crucial aspects of supply chain performance, like procurement negotiation and logistics management, which directly impact manufacturing costs and efficiency. For example, effective negotiation for raw materials can significantly reduce production costs, enhancing market competitiveness.
Understanding SCM in manufacturing is key. It involves a detailed coordination of various activities, emphasizing the importance of streamlining processes to respond to customer needs and market demands. Various supply chain models like lean, agile, and custom-configured are employed to meet these diverse needs. Each model offers unique benefits, such as minimizing waste, enhancing flexibility, or tailoring the supply chain to specific business requirements.
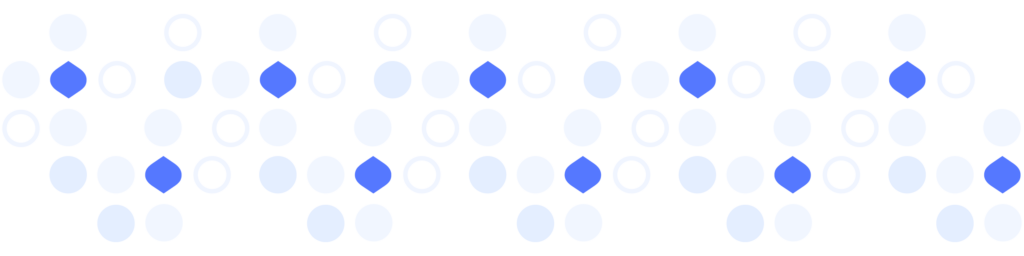
Frequently Asked Questions
1. Why is supply chain management important?
Supply chain management (SCM) is crucial because it oversees the entire flow of goods and services in a business, from the initial sourcing of raw materials to the delivery of the product to the consumer. Effective supply chain management ensures that this process is conducted as efficiently and cost-effectively as possible.
2. In what ways do streamlined business processes and efficient fund transfers impact the final cost of a product?
Streamlined processes and efficient fund transfers can significantly reduce a product’s cost, especially in times of high demand. Manufacturers can avoid delays and additional costs associated with inefficiencies in various supply chain processes by optimizing financial operations.
This optimization includes reducing holding costs in inventory and ensuring the timely delivery of materials, which is crucial for maintaining product quality. Lower operational costs and increased efficiency ultimately lead to a more competitively priced final product without compromising on quality.
3. What role does efficient fund transfer play in the overall supply network of a manufacturer?
Efficient fund transfer is vital for the smooth operation of a manufacturer’s network. It ensures that all entities involved, from suppliers to transportation companies, are paid on time.
This timeliness is crucial for the uninterrupted flow of materials and services, ultimately affecting the production schedule and delivery of the product.
4. How does supply chain management affect the operation of distribution centers in the manufacturing process?
Supply chain management is crucial in efficiently operating distribution centers within the manufacturing process. Effective supply chain management ensures that a distribution center is well-stocked with the right products at the right time, facilitating seamless movement of goods from manufacturing to the end consumer.
It involves coordinating with various supply chain elements, including suppliers and transportation businesses, to ensure that raw materials and final products are transported efficiently and stored properly. This coordination helps minimize delays, reduce inventory costs, and ensure products are available to meet demand.
Good supply chain management leads to optimized distribution center operations, which is key to maintaining a smooth and responsive manufacturing process.