The food and grocery sector relies on a complex supply chain to deliver essential goods. This supply chain is challenged by the perishable nature of many products, leading to food waste, which impacts the environment and the economic health of businesses in this sector.
Proper inventory management techniques are crucial to overcoming these challenges, ensuring the supply chain remains efficient and sustainable.
Combating Food Waste: How Inventory Management Optimizes the Grocery Supply Chain
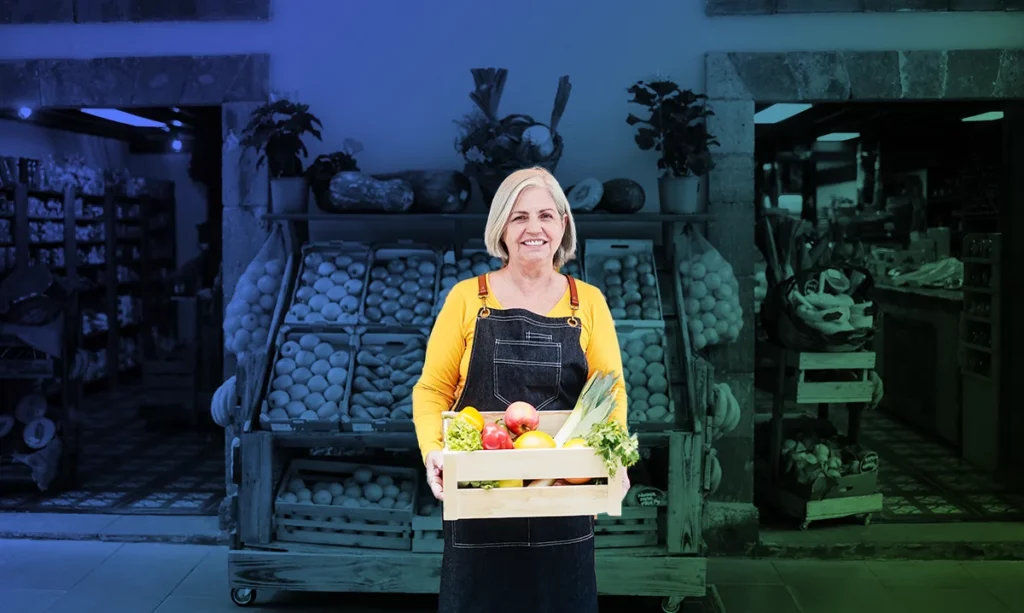
Beyond impacting order fulfillment, inefficiencies within the grocery and food supply chain have far-reaching consequences. Food waste emerges as a major concern, affecting the environment and financial stability.
A 2022 report by the United Nations Food and Agriculture Organization (FAO) highlights the severity of this issue, estimating that roughly 14% of food produced globally is lost or wasted each year. This translates into billions of dollars in annual losses across the food supply chain.
A 2023 study by the University of California, Davis, highlights a link between delayed payments and increased spoilage rates. One key culprit behind this food waste problem is poor inventory management, often exacerbated by slow and inefficient payment processes.
To minimize financial risk, retailers may order perishables less often, leading them to prefer items with longer shelf lives. This practice results in older inventory and higher spoilage rates, negatively impacting the food industry, affecting business operations and causing financial losses for both stores and suppliers.
Balancing Operations and Finances in the Grocery Supply Chain
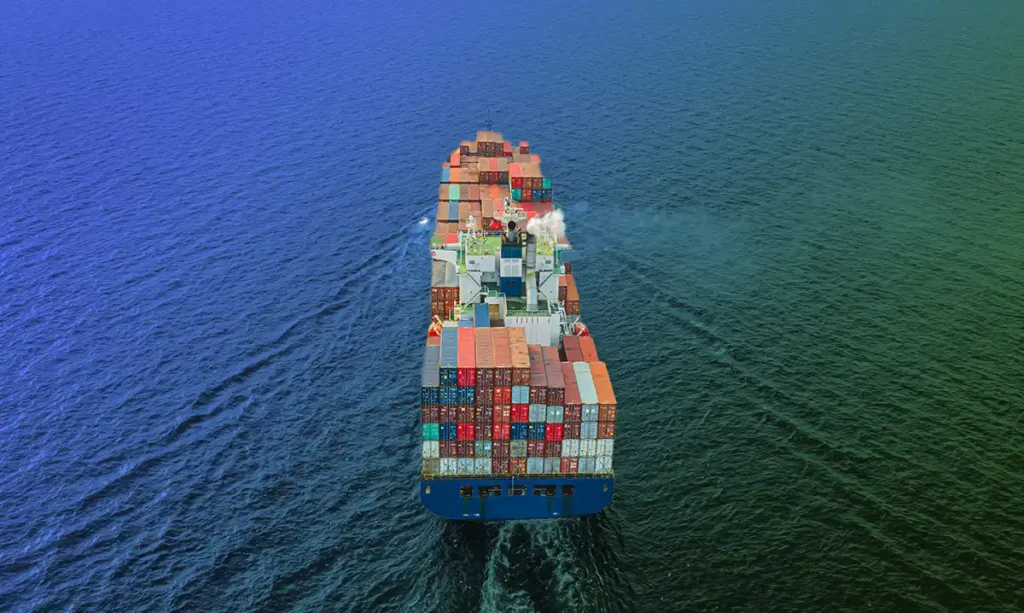
The food journey, from farm to table, involves a complex web of operations and financial considerations. Understanding these intricacies is crucial for a successful and efficient food supply chain.
Ensuring a smooth flow of goods requires robust inventory management practices. A perpetual inventory system continuously tracking stock levels is key to achieving this. This real-time data allows for better order management and informed decisions about future needs.
Effective inventory management techniques, like just-in-time (JIT) delivery models, minimize the need to hold excess inventory. This reduces waste from spoilage, particularly for perishable items, and ultimately lowers total costs.
Using efficient inventory management software is crucial for optimizing the supply chain and controlling these costs.
Regulations and Compliance
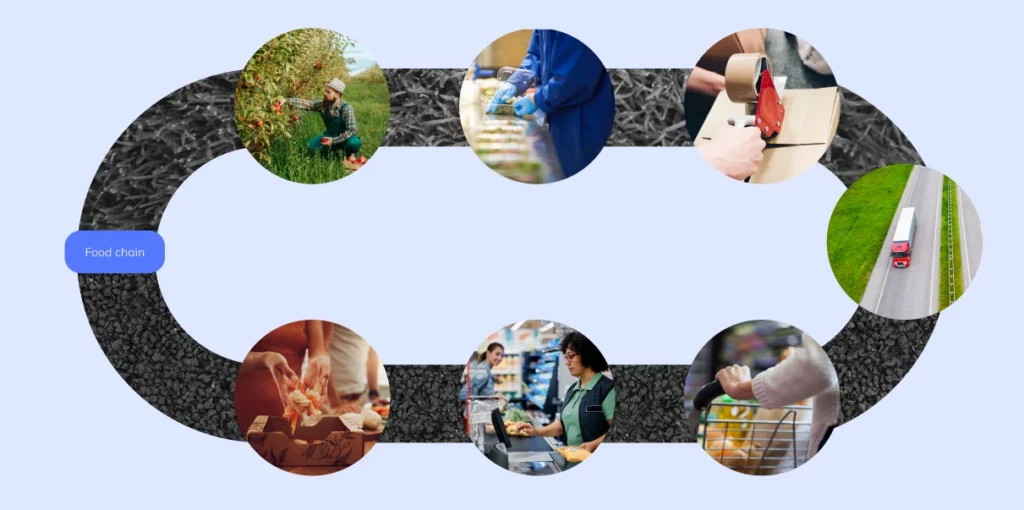
Understanding regulations like Incoterms (international trade terms) and customs requirements helps avoid delays, extra costs, and even legal trouble.
By being familiar with these regulations, businesses can keep their food supply chain efficient, minimize costs, and ensure timely product delivery.
Risk Mitigation
Strategies such as cargo and trade credit insurance play a pivotal role in safeguarding against the risks inherent in the food supply chain.
These measures protect against the loss or damage of goods in transit, including potential breaks in the cold chain for perishable goods like dairy products.
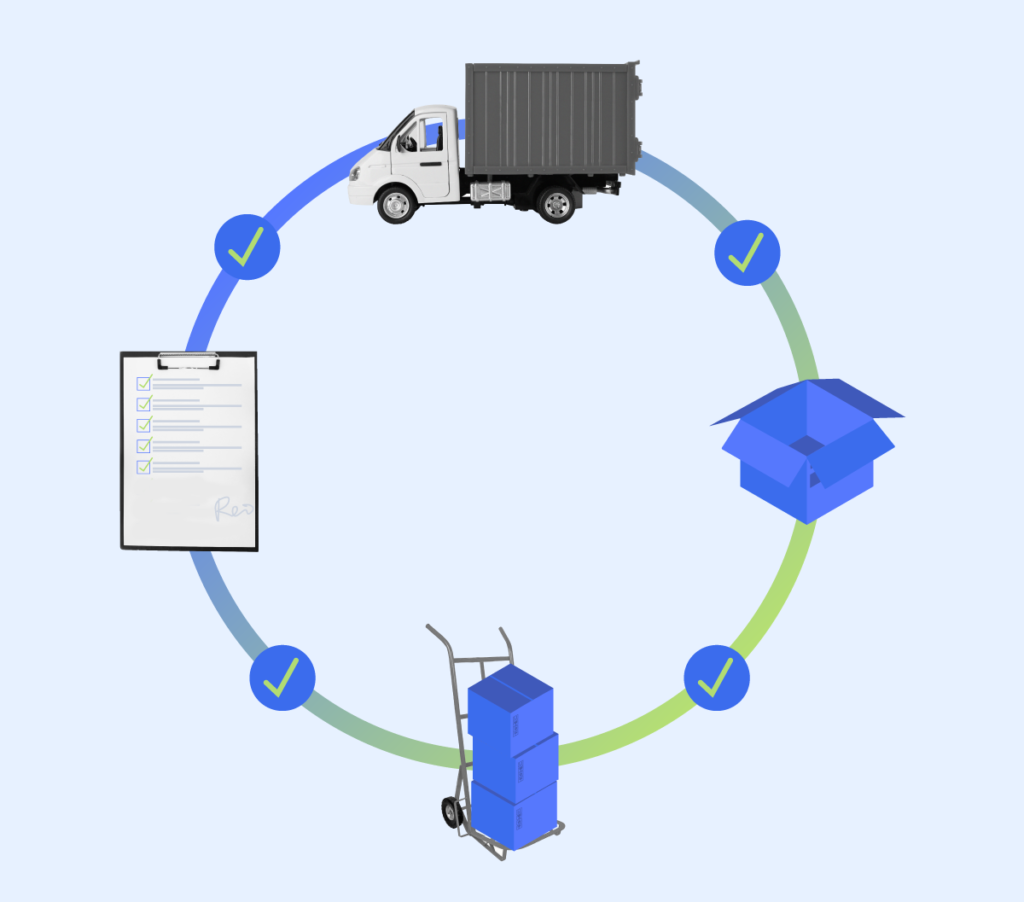
Partner selection, including freight forwarders and customs brokers, is crucial in managing these risks and ensuring the integrity of food safety standards and the economic order quantity of shipments.
Currency Exchange & Costs in International Grocery and Food Supply Chains
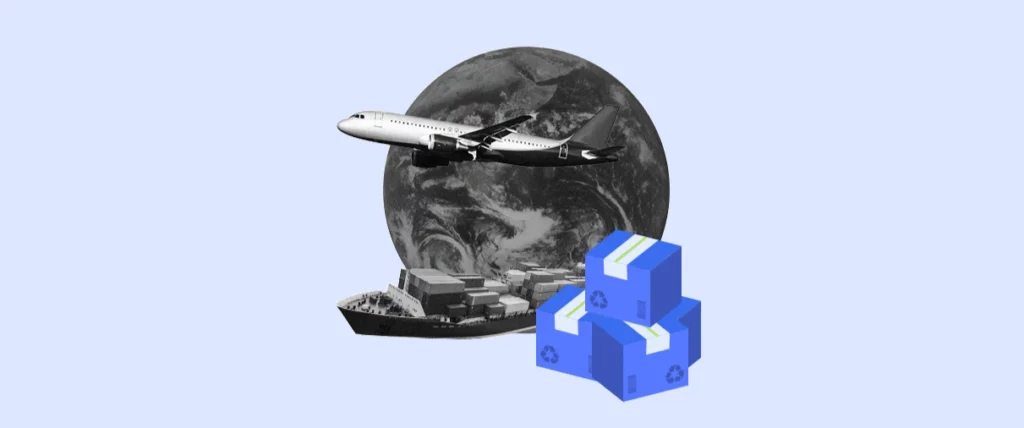
Understanding exchange rates is critical in managing the financial health of food supply chains. Fluctuations can significantly impact profit margins, particularly when dealing with international raw materials and food product suppliers.
Specialized foreign exchange (FX) providers offer a strategic advantage with better rates and lower costs than traditional banking institutions, aiding in the effective management of inventory costs.
Strategic Payment Methods for International Grocery and Food Supply Chains
Choosing the right payment method significantly impacts international grocery and food supply chains, influencing everything from cash flow to inventory.
A diversified approach to payment methods isn’t just a strategy, it’s a necessity that directly affects the efficiency and resilience of the entire supply chain. Here’s a breakdown of some common payment methods and their impact on key areas:
Letters of Credit (L/C)
- Pros: High security for both buyer and seller, promotes trust in international trade.
- Cons: This impacts the buyer’s cash flow due to holding funds until conditions are met.
Documentary Collections
- Pros: Simpler and less expensive than L/C, maintains some security through bank involvement.
- Cons: Requires careful inventory and cash flow management to align with payment schedules.
Open Account Transactions
- Pros: Most flexible option, improves the buyer’s cash flow and inventory turnover.
- Cons: Higher risk for the seller, requires strong buyer-seller relationships and good inventory management.
Advance Payment
- Pros: Favorable for the seller, securing immediate funds. Can be strategically used to secure critical inventory or discounts.
- Cons: The least favorable for the buyer impacts cash flow and potentially jeopardizes reserves.
Adapting Payment Strategies for Global Operations
International food supply chains need a smart approach to payment methods. This considers a company’s finances, supplier relationships, and global market conditions.
Using a mix of payment methods can lower risks, improve cash flow, and guarantee a steady inventory flow. This is vital to meet customer needs and stay competitive globally.
Bringing Operational and Financial Strategies Together
Managing food supply chains effectively requires a big-picture view that combines inventory management, financial planning, and risk reduction.
Tools like data dashboards and flexible payment scheduling help with strategic decisions. This ensures inventory plans align with financial goals. By doing this, businesses can:
- Respond to customer demand efficiently
- Maintain food safety standards
- Navigate the challenges of global supply chains
Efficient management also helps reduce excess stock, maintain optimal inventory levels, and ensure timely restocking of raw materials and finished products.
Businesses that follow lean manufacturing principles can minimize waste and improve their ability to fulfill orders, ultimately contributing to a more sustainable and efficient food industry.
Faster Payments, Fresher Food: How Streamlined Payments Improve Inventory Management
In food supply chains, managing inventory efficiently is crucial. Just-in-Time (JIT) delivery systems, supported by fast payment options like Bancoli’s Global Business Account, offer a powerful solution to common challenges.
By minimizing the amount of food stored at any given time, JIT reduces the risk of spoilage—a major concern in food production and supply. This approach relies on a smooth cash flow to ensure timely restocking of perishable items.
For grocery stores and other business models in the food supply chain, JIT is particularly relevant because of their frequent restocking needs. Of course, accurate predictions of customer demand are still essential for optimizing inventory management.
Freshness Guaranteed: Real-Time Inventory Systems for Optimal Food Supply Chain Management
Access to immediate funds facilitates more frequent orders, significantly reducing spoilage and perfectly embodying JIT principles. This critical adjustment in inventory management enables optimal inventory levels, ensuring that food products are fresh and waste is minimized.
Implementing an inventory system supported by real-time transactions and instant invoice settlements, as provided by Bancoli, empowers businesses to operate with an efficient perpetual inventory management process that aligns closely with supply chain management best practices.
Optimizing Inventory Management for Variety and Cost-Effectiveness
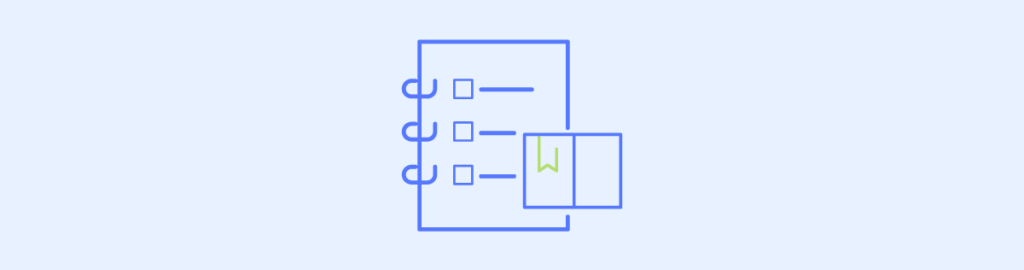
This approach merges the focus on consumer demand and supplier relationships to balance offering variety and minimizing inventory costs.
By aligning payment terms with inventory cycles and utilizing tools like economic order quantity (EOQ) and reorder point formulas, businesses can ensure they have the minimum order quantity of fresh goods to meet consumer demand without incurring excess inventory or waste.
Additionally, prompt payments foster trust with suppliers, leading to a consistent supply of raw materials and finished products.
Optimizing the Food Supply Chain with ABC Analysis Strategy
To effectively optimize the food and grocery supply chain, incorporating an ABC analysis strategy into your inventory management process can significantly enhance operational efficiency and profitability.
Efficient payment processes and cash flow management are crucial for implementing such a strategy.
Here’s how businesses in the food and grocery industry can leverage this approach:
Step 1: Laying the Foundation: Data-Driven Inventory Management for Optimal Stock Levels
Effective inventory management hinges on a data-driven approach. This initial step involves gathering and analyzing crucial information about each inventoried item, including details like annual consumption value, turnover rate, and perishability.
This data is often readily available within an existing inventory management system or Enterprise Resource Planning (ERP) software.
Next, leverage external tools or software capable of performing ABC analysis. This analytical technique categorizes the inventory items into three groups based on their consumption value and other relevant criteria:
- Category A: High-value items with a significant impact on overall inventory costs, though typically lower in quantity. Given these items’ importance, ensuring a reliable cash flow for timely restocking is essential, which is where Bancoli’s quick payments processing is considerably beneficial.
- Category B: Items with moderate value and quantity. Here, a balanced approach is key. Implement regular monitoring and maintain moderate inventory levels to optimize turnover without overinvesting.
- Category C: Low-value items, usually high in quantity but with minimal impact on total inventory costs. For these items, steady replenishment is important based on consumption forecasts.
Step 2: Enhancing Supplier Relationships and Payments
Utilize Bancoli’s Global Business Account to manage multi-currency transactions efficiently with international suppliers. This ensures that you can negotiate and settle payments most cost-effectively. This is particularly crucial for Category A items, where cost savings directly impact the bottom line.
Implement dynamic payment scheduling to align with your inventory replenishment strategy, ensuring that payments are processed in sync with your inventory cycle, especially for high-priority A items. This helps maintain healthy supplier relationships and secures better terms and supply reliability.
Step 3: Continuous Improvement and Adaptation
Review the ABC categorization regularly to adjust for changes in consumer demand, supplier performance, and market conditions. This dynamic approach ensures that your inventory strategy aligns with business objectives and market demands.
Leverage insights from Bancoli’s real-time transaction visibility to monitor cash flow and payment efficiency, adapting your strategy to meet financial and operational goals.
You can achieve a more streamlined, cost-effective, and responsive inventory system by integrating an ABC analysis strategy into your food supply chain management while leveraging Bancoli’s efficient payment processing and cash flow management features. This strategic approach enables businesses to focus their resources where they matter most, improving overall supply chain resilience and customer satisfaction in the competitive food and grocery industry.
How can JIT and ABC work together?
The integration of Just-In-Time (JIT) and ABC analysis methodologies presents a strategic approach to inventory management. The synergy between these two methods enables businesses to refine their inventory practices, ensuring they maintain an optimal balance of stock.
Prioritization in Inventory Management
Identifying and prioritizing inventory is crucial. ABC analysis plays a pivotal role by categorizing products based on their importance and turnover rate. This method enables businesses to strategically apply Just-In-Time (JIT) methodologies for effective inventory management based on the ABC categorization.
Targeted Inventory Management for A-Items
For items classified as high-value and high-demand (A-items), the principles of JIT are particularly beneficial. This approach advocates ordering such products in smaller quantities but more frequently, thereby minimizing holding costs. It ensures that customer demand is promptly met without facing the repercussions of spoilage or overstocking, which are common challenges in managing perishable goods.
Adapting Strategies for B and C Items
While A-items receive the most focus under JIT principles, B and C items benefit from a different approach. Given the less predictable demand or lower spoilage risk associated with these products, businesses might opt to maintain a slightly larger buffer stock, offering more flexibility in inventory management.
Key Considerations for Implementing JIT and ABC Analysis
For Just-in-Time (JIT) strategies to succeed, the emphasis on punctual deliveries and robust logistics is critical. It’s essential for grocery retailers to establish solid relationships with reliable suppliers, ensuring consistent adherence to delivery timelines.
Improving Forecasting for Demand
The effectiveness of JIT systems in managing perishables hinges on the accuracy of demand forecasting. Precision in anticipating sales is crucial to avoid out-of-stock scenarios and maintain optimal inventory levels.
Technological Upgrades for Efficiency
Integrating JIT with Activity-Based Costing (ABC) analysis requires grocery businesses to embrace advanced technologies for inventory management and demand forecasting. Utilizing sophisticated systems helps in tracking inventory accurately and forecasting sales with greater precision.
Planning for the Unpredictable
Despite meticulous planning and forecasting, the JIT approach can be vulnerable to unforeseen supply chain disruptions. Grocery stores and food related business models need to develop robust contingency plans to ensure that sudden disruptions don’t result in inventory shortages or affect customer satisfaction.
Bancoli’s Role in the Food and Grocery Industry
Bancoli’s Global Business Account is a strategic asset designed to address the nuanced challenges and opportunities within the food and grocery sector, making operations more efficient and sustainable.
Multi-Currency Support: Bridging the Global Divide
One of the significant hurdles in the food and grocery industry is dealing with international suppliers. Currency fluctuations can significantly impact the cost of raw materials and food products, affecting overall profitability.
Bancoli’s Global Business Account is an essential tool in this regard. It allows transactions in USD, EUR, GBP, HKD, and SGD and payout conversions to JPY, CNY, INR, ILS, and PHP, simplifying the process of dealing with international suppliers and offering a hedge against currency exchange volatility.
Dynamic Payment Scheduling: Synchronizing Cash Flow with Operational Needs
Bancoli helps businesses tailor payment terms to their specific inventory cycles and demand forecasts. By aligning payment schedules with inventory needs, businesses can ensure they have the financial liquidity to restock at the right time, maintaining a balance between supply and demand.
This synchronization between financial flow and operational requirements is vital for minimizing waste and ensuring that consumers can always access fresh and varied products.
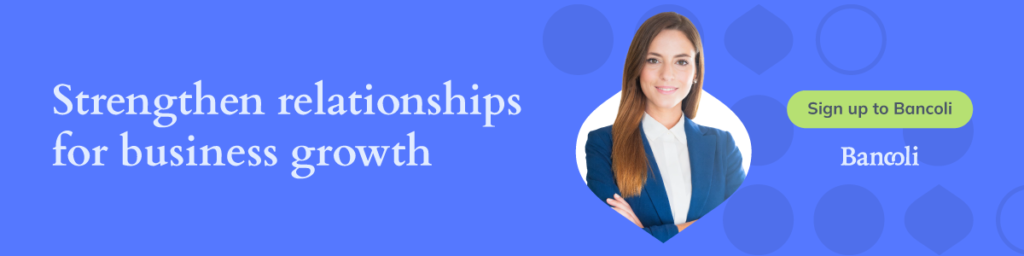
Conclusion: Towards a More Efficient and Sustainable Industry
By refining inventory management practices, ensuring a diverse range of products, and solidifying supplier relationships, businesses can consistently deliver fresh, quality food to consumers.
Implementing efficient payment solutions like Bancoli’s Global Business Account marks a significant step toward optimizing the food and grocery supply chain.
This strategic approach mitigates food waste’s environmental and economic repercussions and propels the industry toward a more sustainable and resilient model.
Embracing streamlined and agile supply chain practices, underscored by efficient payment processes and a solid understanding of supply chain dynamics, is indispensable for the future prosperity of food production, distribution, and consumption.